Content
Introduction to HPMC and Its Benefits
Step-by-Step Guide on Incorporating HPMC in Construction Mixtures
Key Considerations and Best Practices for Using HPMC
Applications and Advantages of HPMC in Various Construction Projects
Subtitle 1: Introduction to HPMC and Its Benefits
HPMC, short for Hydroxypropyl Methylcellulose, is a versatile additive widely used in construction applications. It is derived from cellulose and offers several beneficial properties. HPMC acts as a thickener, a water retention agent, and a binder, providing improved workability, adhesion, and consistency to construction mixtures. Additionally, it enhances the durability and performance of the final product. With its wide range of applications, HPMC has become a popular choice among contractors and builders in the construction industry.
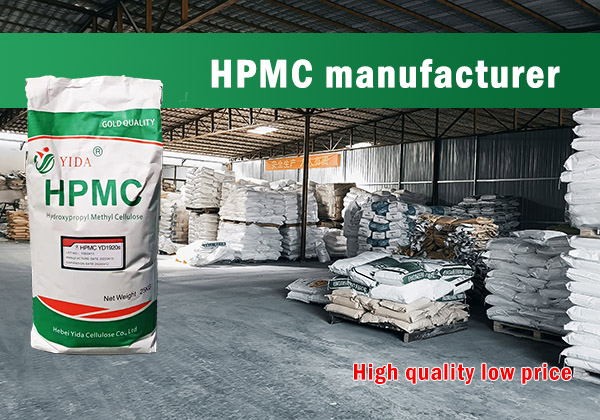
Subtitle 2: Step-by-Step Guide on Incorporating HPMC in Construction Mixtures
When using HPMC in construction mixtures, it is essential to follow a systematic approach to ensure proper dispersion and achieve the desired results. Here is a step-by-step guide to using HPMC effectively:
Step 1: Measure the Required Amount: Start by accurately measuring the recommended amount of HPMC powder based on the specifications provided by the manufacturer or as per the project requirements.
Step 2: Pre-Mix HPMC: Gradually add the measured HPMC powder to clean water while continuously stirring. It is crucial to maintain a consistent and uniform dispersion of HPMC particles in the water.
Step 3: Allow Hydration: After thoroughly mixing the HPMC powder with water, allow it to hydrate for a specific duration as mentioned in the manufacturer's guidelines. During this time, the HPMC will swell and disperse, forming a gel-like substance.
Step 4: Combine with Construction Mixture: Once the HPMC solution has fully hydrated, add it to the construction mixture, such as mortar or concrete. Mix thoroughly to ensure even distribution of HPMC throughout the mixture.
Step 5: Adjust Consistency and Workability: Depending on the desired consistency and workability of the construction mixture, additional water may be added. However, it is important to avoid over-watering, as it can adversely affect the performance and strength of the final product.
Subtitle 3: Key Considerations and Best Practices for Using HPMC
While incorporating HPMC into construction mixtures, it is essential to keep in mind some key considerations and follow best practices. Here are a few recommendations:
Proper Measurement: Accurately measure the required amount of HPMC to ensure the desired properties and performance of the construction mixture.
Mixing Time: Allow sufficient time for the HPMC to hydrate and disperse properly before combining it with the construction mixture. This will ensure optimal performance and consistency.
Mixing Equipment: Use appropriate mixing equipment, such as a mechanical mixer or a paddle mixer, to achieve a uniform distribution of HPMC throughout the construction mixture.
Compatibility Testing: Conduct compatibility tests before using HPMC with other additives or admixtures. This will help identify any potential reactions or conflicts that could affect the performance of the mixture.
Follow Manufacturer's Guidelines: Always refer to the manufacturer's instructions and guidelines for the specific HPMC product being used. This will provide valuable insights into dosage, mixing procedures, and other important considerations.
Subtitle 4: Applications and Advantages of HPMC in Various Construction Projects
HPMC finds extensive application in various construction projects due to its numerous advantages. Some notable applications include:
Tile Adhesives: HPMC enhances the workability and bonding properties of tile adhesives, ensuring improved adhesion and reducing the risk of tile slippage or detachment. It also improves water retention, allowing for better curing and reducing the occurrence of cracks.
Renders and Plasters: HPMC is commonly used in renders and plasters to improve workability, reduce shrinkage, and enhance adhesion to substrates. It provides excellent sag resistance, enabling vertical application without slumping, and contributes to a smoother and more consistent finish.
Self-Leveling Floor Compounds: HPMC is an essential component in self-leveling floor compounds, as it improves flowability and self-leveling properties. It helps to achieve a flat and smooth surface, reducing the need for extensive manual leveling and ensuring even distribution of the compound.
Cementitious Grouts: HPMC is added to cementitious grouts to enhance flowability, improve adhesion, and reduce segregation. It prevents excessive water loss, ensuring proper hydration and strength development of the grout, while also improving resistance to shrinkage and cracking.
The advantages of using HPMC in construction projects include:
a. Improved Workability: HPMC enhances the workability and ease of handling of construction mixtures, making them more malleable and easier to apply or shape.
b. Enhanced Adhesion: HPMC improves the bond strength between different materials, such as tiles and substrates or renders and surfaces, leading to a more durable and long-lasting construction.
c. Water Retention: HPMC acts as a water retention agent, allowing construction mixtures to maintain proper hydration and curing. This helps to prevent premature drying, shrinkage, and cracking.
d. Reduced Shrinkage and Cracking: By reducing water loss during the curing process, HPMC minimizes shrinkage and the formation of cracks, resulting in stronger and more resilient structures.
e. Improved Durability: The addition of HPMC improves the overall durability and resistance to weathering, providing increased longevity to construction projects.
In conclusion, HPMC is a versatile additive that offers numerous benefits in construction applications. By following a step-by-step approach and considering best practices, contractors and builders can effectively incorporate HPMC into their construction mixtures. Whether it's improving workability, enhancing adhesion, or reducing shrinkage, HPMC proves to be a valuable tool in achieving high-quality and durable construction outcomes.
YIDA HPMC cellulose
YIDA Cellulose Co., Ltd. is a Chinese factory specializing in the production of HPMC cellulose. It has 16 production lines and an annual output of 26,000 tons. Our samples support free mailing and testing, and our laboratory can provide experimental data and product deployment.
Contact us to learn more.